American Family Insurance
East Regional Building (ERB)
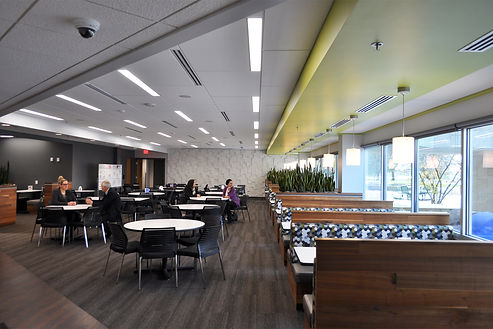
2020 Award of Merit
Innovative Project, Interiors
NOMINATED BY:
Strang, Inc.
LEED RATING SYSTEM:
LEED ID+C: Commercial Interiorsv3 - LEED 2009
LEED CERTIFICATION:
LEED Certified (June 24, 2019)
USGBC PROJECT PROFILE:
https://www.usgbc.org/projects/american-family-insurance-erb
PEOPLE/ORGANIZATIONS ASSOCIATED WITH THE EFFORT FEATURED IN THE NOMINATION:
-
Owner: American Family Insurance
-
Architect/Engineer: Strang Inc.
-
General Contractor: J.H. Findorff & Son Inc.
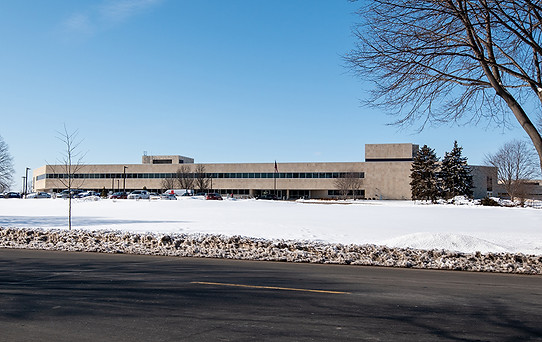
EXECUTIVE SUMMARY:
The American Family Insurance East Regional Building was an interior renovation of a nearly 200,000 square foot office building. Sustainability is a driving value at American Family Insurance and this project truly showcased those values. American Family took advantage of some of the industry’s most efficient envelope materials, HVAC systems, and lighting systems in order to achieve an overall 32% reduction in energy costs. Additionally, the project underwent an intensive commissioning process under the direction of two separate firms that not only augmented the Architectural-Engineering and Construction Administration services but also contracted third-party, independent commissioning. Lastly, the building location lends itself to many walkable amenities for employees, furthering their culture of community connectivity.
NOTABLE SUSTAINABLE STRATEGIES USED IN THE PROJECT:
The American Family East Regional Building was an interior renovation of a nearly 200,000 square foot office building. Sustainability was the driving factor in the design and construction process of this project and a goal of achieving LEED Silver certification was established at the outset. Early decisions were made to invest in higher performing fenestration systems, HVAC systems, and lighting systems. In addition, a complete overhaul of the Building Automation System and DDC was included in the project to modernize energy saving strategies through high performance sequences of operation.
American Family selected Strang as their Architect/Engineer and partnered with Findorff as their General Contractor following the Integrated Project Delivery model. All design and construction disciplines were able to collaborate thoughtfully throughout the project. In the end, due to these collaborative efforts, the team exceeded the sustainability goals and ended up achieving LEED Gold certification for the project.
A large focus of the project was to save as much as the existing building structure/envelope as possible, improve the occupant experience, densify the occupancy of departments, and reduce energy consumption. To achieve this, the project determined that the entire building structure and concrete systems could be retained, along with the main HVAC ductwork. The existing HVAC systems were identified as being a major contributor to energy consumption, and with new occupant densification and a 30% increased ventilation, the building's main air distribution fans were replaced with those of higher efficiencies along with central heating boilers. Energy analysis helped justify replacement of all exterior glazing and new digital controls were furnished for all HVAC equipment to holistically optimize the operations. The project installed carbon-dioxide sensors for a zone and system-level demand-controlled ventilation strategy that reduces the volume of fresh air when indoor air quality is acceptable. The changes resulted in more than a 30% reduction in HVAC energy costs compared to code. The project upgraded lighting and controls, resulting in a 62% reduction in connected lighting power with daylighting and task lighting control strategies that allow lighting to be reduced to suit occupants’ comfort while saving energy. Major building equipment that was Energy Star eligible, such as appliances in the project’s full-service cafeteria, were selected as such resulting in over 53% Energy Star-rated equipment. Occupant health was a major factor in choosing construction materials, with all wood products containing no added urea-formaldehyde resins and mandating low VOC content in adhesives, paints, coatings and flooring products. Lastly, it was important to American Family to be mindful of sustainability as it related to the construction process. Over 75% of on-site generated construction waste was diverted from landfills while over 33% of total building-material content manufactured used recycled materials.
CHALLENGES FACED BY THE PROJECT TEAM:
When it comes to the sustainability aspect for renovating existing facilities vs. building new, the case for saving the existing carbon footprint is attractive, but at significant cost. The ERB project unfolded as 14 back-to-back phases of staged renovation in an occupied building that was to begin shifting operations from two of their three shifts. Under those conditions, the major challenges were the replacement of the entire electrical and communications systems, and most of the HVAC distribution. The planning required intense and detailed efforts to ensure the core functions of the building were kept online or redirected around the work as new equipment was installed. The project continued to strive to reuse and utilize existing systems where possible, radiant heat and some distribution ductwork being two examples.
Another challenge of the project was maintaining chiller plant operation while chiller plant controls underwent renovation. The building’s central utility plant contains (3) 350-ton chillers that serve occupied areas of the building and critical data center operations. The chiller controls underwent a migration to a new direct digital control system and the project included optimizing all sequences of operation. Careful planning and pre-programming were essential to help with the transition and “all hands were on-deck" during the switchover to ensure any unforeseen circumstances could be addressed immediately. Thorough functional performance testing was executed for the central utility plant to ensure optimal operations.
